Navigating the intricate world of high-quality cryogenic differential pressure gauges unveils a niche yet crucial aspect of industrial instrumentation. These devices, designed to measure pressure differences in extremely cold environments, serve as essential components across various industries, including aerospace, petrochemical, and medical fields. Through understanding their functionality, applications, and benefits, businesses can harness these tools to optimize complex operations and ensure significant advancements in efficiency and reliability.
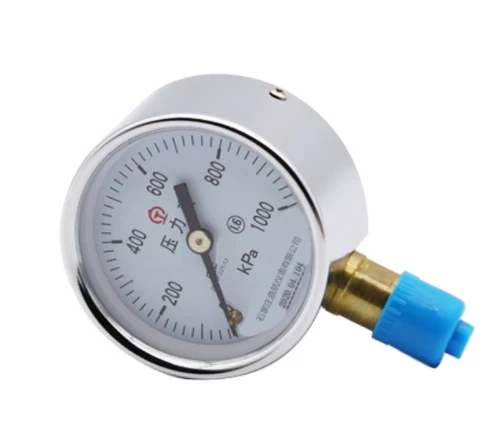
High-quality cryogenic differential pressure gauges operate effectively under frigid conditions where standard gauges would fail. The technology behind these gauges is predicated on materials and components specifically engineered to withstand temperatures often plummeting below -150°C. At these temperatures, conventional mechanisms may seize or provide inaccurate readings due to the contraction of materials. However, cryogenic gauges utilize special alloys and advanced designs to maintain accuracy and performance integrity.
In the aerospace and avionic sectors, cryogenic environments are commonplace, particularly during high-altitude flights or within spacecraft. Here, differential pressure gauges play a pivotal role in monitoring the pressure differences between various compartments to ensure cabin safety and the optimal performance of onboard systems. Accurate pressure readings in these applications are non-negotiable, as even minor discrepancies can lead to catastrophic failures.
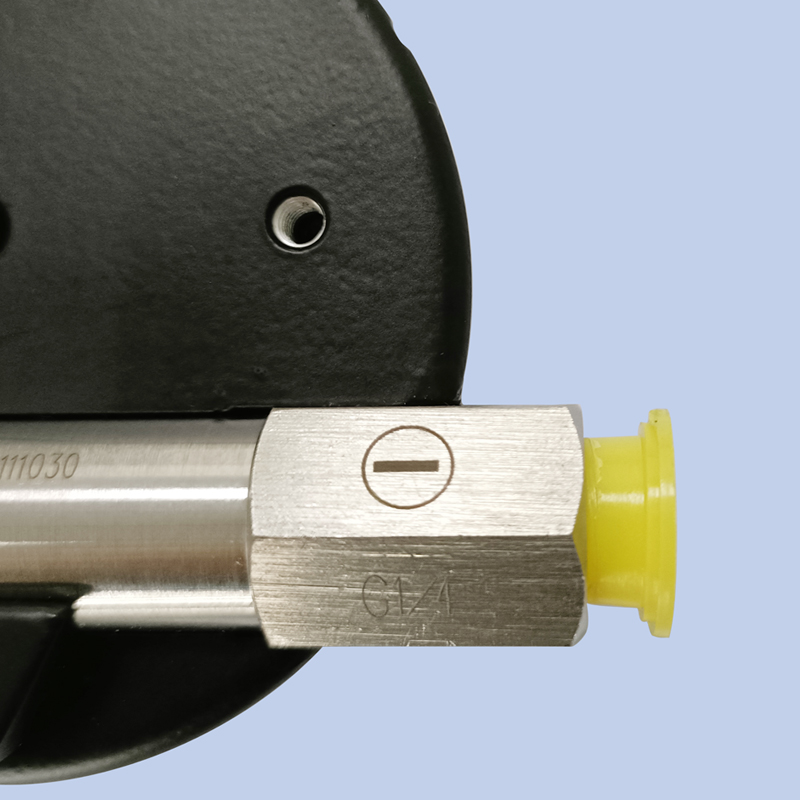
The petrochemical industry also demands precision in cryogenic measurement, especially in the realm of liquefied natural gas (LNG) storage and transport. With LNG being stored at approximately -162°C, any pressure variations within storage tanks must be constantly monitored to prevent leaks, structural damage, or potential explosions. Cryogenic differential pressure gauges offer the precise and reliable measurements necessary to maintain safety standards and operational continuity in processing plants and transport vessels.
Medical applications further showcase the versatility and necessity of these specialized gauges. In the storage and handling of cryogenic materials like liquid nitrogen, which is extensively used in cryopreservation and certain medical treatments, monitoring pressure differentials is essential. Ensuring the correct pressure conditions helps maintain the integrity and stability of biologically sensitive materials, safeguarding both patients and medical outcomes.
high quality cryogenic differential pressure gauge
The benefits of employing high-quality cryogenic differential pressure gauges extend beyond just precision. One of their most significant advantages is the promotion of operational efficiency. By providing real-time pressure data, these gauges facilitate predictive maintenance strategies, allowing for timely interventions before minor issues escalate into costly downtime or repairs. Additionally, the reliability of these instruments reduces the need for constant manual checks, freeing up resources and labor for other critical tasks.
From an expertise standpoint, selecting the right type of cryogenic differential pressure gauge requires a comprehensive understanding of the application-specific demands. Variables such as the required pressure range, environmental conditions, and the materials being monitored must all be considered. Manufacturers of these gauges often provide detailed consultations and customization options to ensure the selected product integrates seamlessly into existing systems.
In terms of authoritativeness, leading manufacturers in the field of cryogenic instrumentation continue to innovate and push the boundaries of what these gauges can achieve. Collaborations with research institutions and continued advancements in material science are paving the way for more robust and adaptable designs. This evolving landscape reinforces the credibility and authority of well-established brands that consistently deliver superior products tailored to the nuanced needs of modern industries.
Trustworthiness in cryogenic differential pressure gauges is established through rigorous testing and certification processes. Adherence to international standards, such as those set by the International Organization for Standardization (ISO) and the American Society of Mechanical Engineers (ASME), ensures that these gauges meet or exceed the stringent requirements for performance and safety. Customers can trust that their chosen instruments will perform reliably even in the most demanding conditions.
In conclusion, the world of high-quality cryogenic differential pressure gauges is vast and layered with complexity, demanding a blend of scientific innovation and practical application. As industries continue to evolve and explore new frontiers, the importance of precision in low-temperature environments cannot be overstated. With the assurance of expertise, authority, and trust, businesses can confidently leverage these instruments to drive forward their operational excellence and technological innovation.