High-quality static pressure measurement in differential pressure gauges is crucial to ensuring accurate, reliable readings in various industrial applications. Utilizing the right technology and expertise in this domain fosters trust in the instruments and the data they provide, offering significant benefits across fields such as HVAC, process industries, and fluid mechanics. This depth of dependability and precision helps facilities maintain system integrity, safety, and efficiency.
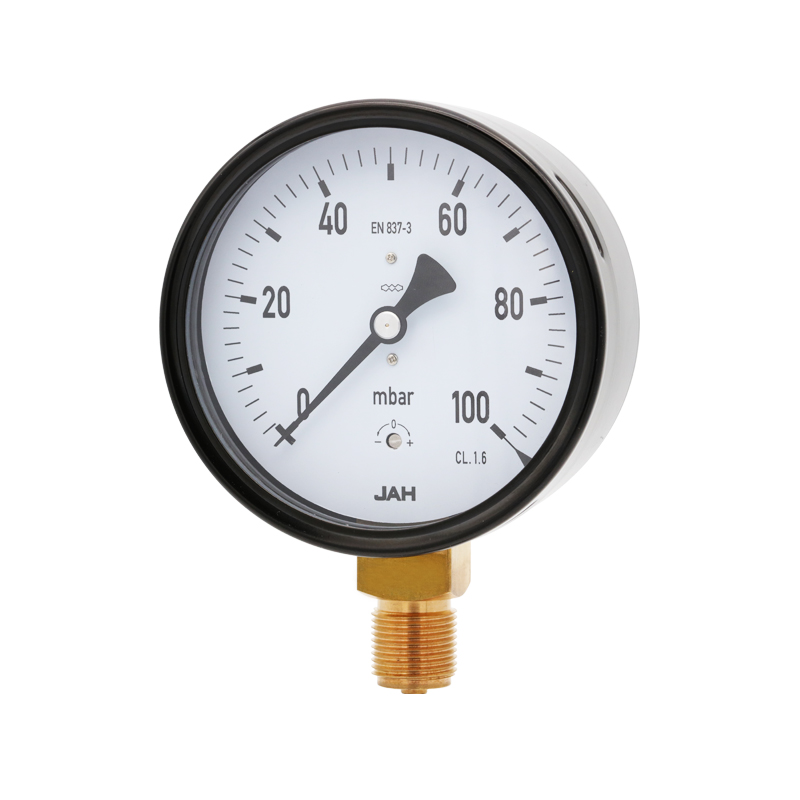
Static pressure, a fundamental aspect in differential pressure measurement, refers to the pressure exerted by a fluid at rest. In an industry context, it determines the resilience of systems to withstand various operational challenges. High-quality static pressure in differential pressure gauges is central to process optimization because it serves as the bedrock for accurate differential pressure readings, which in turn inform critical decisions on system control and efficiency.
A differential pressure gauge measures the difference in pressure between two points, often using a diaphragm or a similar mechanical element that senses the pressure variation. High-quality instruments ensure that changes in static pressure do not lead to calibration errors or inaccuracies, which could potentially disrupt operations or lead to unsafe conditions. For example, in HVAC systems, precise static pressure measurement enables the fine-tuning of airflow and ventilation, ensuring environments remain comfortable and energy-efficient.
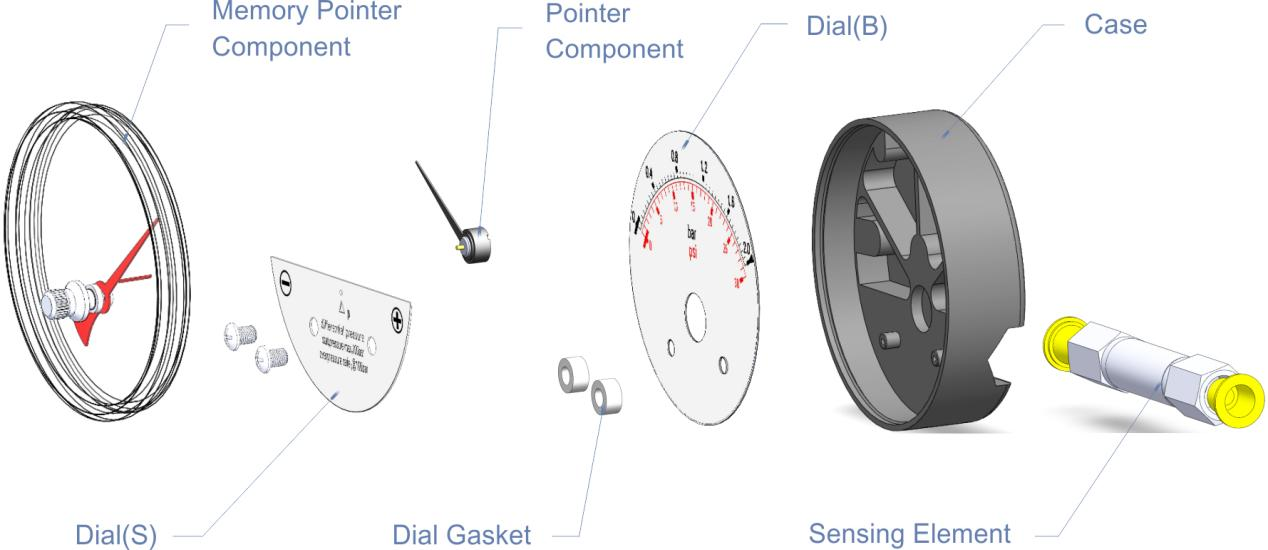
To deliver on Experience, Expertise, Authoritativeness, and Trustworthiness, manufacturers of differential pressure gauges integrate state-of-the-art technology and adhere to stringent industry standards. Materials used in constructing these instruments must resist corrosion and extreme temperature variations, thereby ensuring longevity and reliability. Certification and compliance with international standards such as ISO or ASME likewise affirm the instrument's quality and reliability.
high quality static pressure in differential pressure gauge
Expertise is critical in this realm, with continual advancements in sensor technology and manufacturing processes enhancing the performance of pressure gauges. For instance, incorporating ceramic or silicon sensors can drastically improve the accuracy of static pressure readings by minimizing temperature and humidity effects. Furthermore, digital advancements allow for real-time monitoring and data logging, bringing a new level of oversight and flexibility to system managers and engineers.
Authoritativeness is established through rigorous testing and performance validation, along with the publication of empirical data demonstrating the instrument's capabilities in a variety of conditions. Technical datasheets and white papers often provide in-depth insights into the measurement technology, offering an authoritative source for engineers and procurement specialists seeking to make informed purchasing decisions.
Trustworthiness in differential pressure gauges is achieved through transparency and customer support. Leading manufacturers provide extensive warranties and offer customized calibration services to sustain the accuracy of these instruments throughout their lifecycle. By building strong customer relationships and maintaining open lines of communication for troubleshooting and maintenance guidance, they establish a solid foundation of trust.
In summary, high-quality static pressure in differential pressure gauges is a testament to technological advancement, meticulous manufacturing, and a commitment to reliability and precision. Through the amalgamation of experience, expertise, authority, and trust, these instruments empower industries to optimize their operations and safeguard their processes. Whether employed in controlling HVAC systems or ensuring the smooth operation of industrial processes, reliable static pressure measurements are indispensable to efficiency and safety.