An analogue differential pressure gauge stands as an indispensable tool in a myriad of industrial applications. Its relevance stems not only from its simplistic design but also from its precision in providing real-time monitoring and control of pressure differences across various systems. Having worked extensively with these devices, my amassed experience underscores their crucial role in promoting optimal system performance and maintaining safety standards.
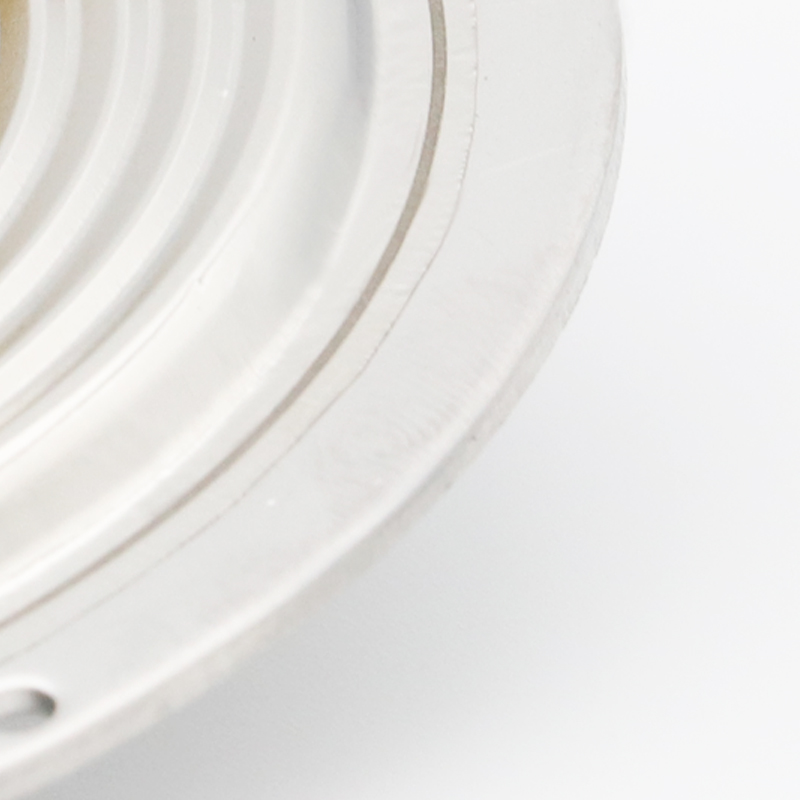
Expertise in selecting the correct analogue differential pressure gauge requires a thorough understanding of the specific application it is intended for. Different industries may demand varying levels of sensitivity and accuracy. For instance, in the chemical processing industry, where accuracy is paramount, selecting a gauge with a high precision level is essential. This can prevent costly mishaps, ensure regulatory compliance, and maintain efficient process operations. My expert recommendation would be choosing a gauge that not only meets your immediate needs but also anticipates potential future adjustments in the process parameters.
Authoritativeness in the domain of analogue differential pressure gauges can be attributed to understanding the nuances of gauge designs, material choices, and application environments. Gauges with stainless steel casings, for instance, are ideal for harsh environments due to their corrosion resistance. In contrast,
aluminum casings may be more suitable for less aggressive settings. Moreover, understanding the diverse types of pressure elements—such as diaphragms, bellows, and Bourdon tubes—can guide users in selecting the most appropriate gauge for their specific requirements. Throughout my career, I've observed that investing in a higher-quality gauge often yields long-term savings by minimizing downtime and reducing maintenance costs.

analogue differential pressure gauge
Trustworthiness is a cornerstone of effective use and deployment of analogue differential pressure gauges. It is imperative for users to regularly calibrate their gauges to ensure continuous accuracy. Calibration should be performed under controlled conditions, ideally using a reference gauge of known accuracy. Furthermore, understanding potential failure modes—such as fatigue of the pressure element or mechanical wear—and implementing regular maintenance schedules can mitigate unexpected operational failures. Trust in a gauge’s performance thus often correlates directly with meticulous attention to regular upkeep and periodic review of performance data.
Real-world experience reveals frequent misconceptions about the operational capabilities of analogue differential pressure gauges. A common misunderstanding is underestimating the impact of temperature variations on gauge accuracy. Installing the gauge with adequate thermal insulation or temperature dampening materials can significantly enhance accuracy in environments with fluctuating temperatures. Another frequent oversight is neglecting to accommodate pressure surges, which can overstress gauge components and lead to premature failures. Utilizing gauges with integrated pressure dampeners or snubbers can effectively manage these pressure spikes, prolonging the lifespan of the device and ensuring consistent performance.
In conclusion, the analogue differential pressure gauge, though seemingly simplistic, embodies a confluence of engineering precision, material science, and practical experience. Employing these gauges effectively demands a cognizant approach to selecting, maintaining, and understanding their functional dynamics. Through adherence to best practices and remaining abreast of technological advancements, users can harness the full potential of these indispensable instruments, thereby securing their operational integrity and performance reliability.