Differential pressure gauges play a pivotal role in various industrial applications, providing critical insights into system efficiencies and operational safety. These devices, designed to measure the pressure difference between two points in a system, are quintessential for processes where precision matters. Understanding their functionality, selection criteria, and applications can enhance your operational capabilities significantly.
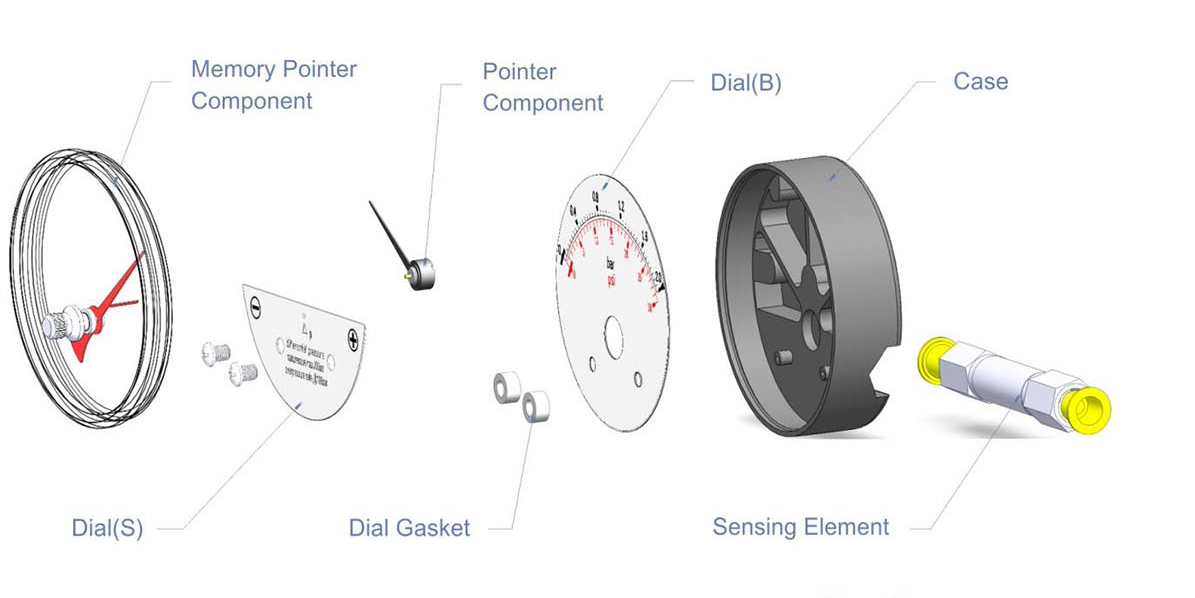
To appreciate the utility of differential pressure gauges, one must first comprehend their operational principle. At their core, these gauges employ a diaphragm sensor that deflects when there is a pressure disparity between its two sides. This deflection is then translated into a readable scale, offering a precise measurement of pressure differences. This ensures accurate readings for applications ranging from HVAC systems to filtration processes in chemical manufacturing.
When selecting a differential pressure gauge, several factors underline the decision-making process. The first consideration should be the working pressure range of the system. Selecting a gauge that meets or exceeds this range ensures durability and reliability. Additionally, material compatibility is crucial. The gauge materials must withstand the chemical composition of the mediums involved to prevent degradation.
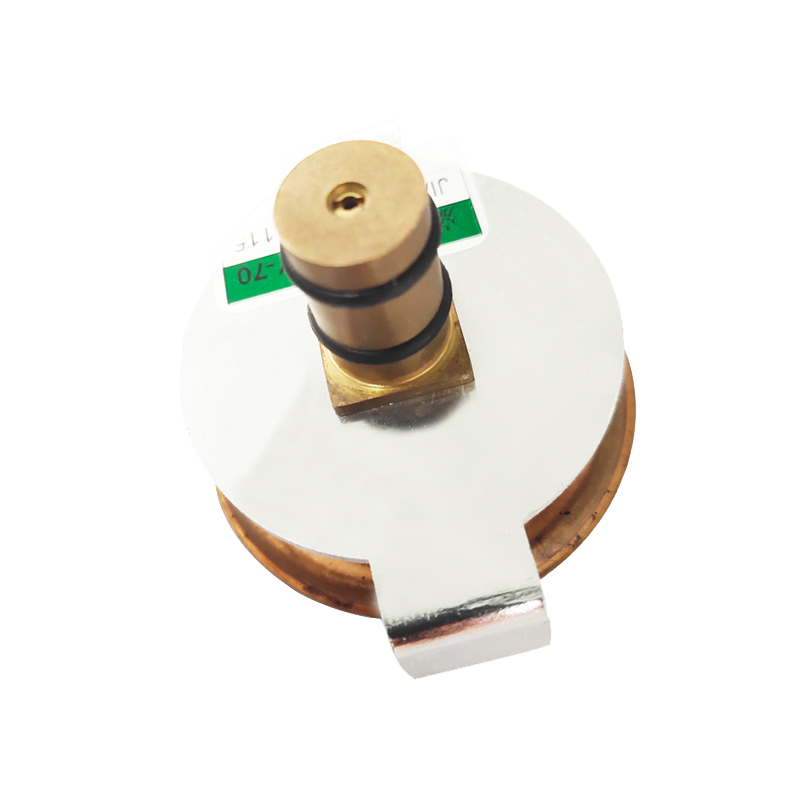
Accuracy requirements also demand attention. Depending on the sensitivity needed, gauges with higher accuracy levels might be essential, particularly in critical applications such as pharmaceutical production or aerospace engineering. Furthermore, the gauge's environmental resistance, including factors like temperature, humidity, and exposure to corrosive elements, should align with the site conditions.
One of the most compelling applications of differential pressure gauges is in filter monitoring systems. By measuring the pressure drop across filters, these gauges provide real-time data to determine when a filter is clogged and needs replacement. This not only ensures the system's operational efficiency but also prevents damage or underperformance caused by inadequate filtration.
differential pressure gauge,
Furthermore, in the realm of energy management, differential pressure gauges aid in optimizing HVAC systems. They help monitor air ducts and coil blockages, ensuring the system operates at peak efficiency, which leads to reduced energy consumption and cost savings. Such applications underline how these gauges contribute to sustainability efforts and operational efficiency.
In the chemical industry, differential pressure gauges ensure that reactors operate under precise conditions, which is critical for maintaining product quality and safety. By constantly monitoring pressure discrepancies, engineers can adjust parameters to avert hazardous situations. This level of control underscores the importance of these instruments in maintaining safety standards and compliance with regulatory requirements.
The dependability of differential pressure gauges also extends to water treatment facilities. By measuring pressure differences across membranes in reverse osmosis systems, these gauges ensure membranes are clean and functioning efficiently, which is crucial for producing high-quality, safe water.
In terms of maintaining trustworthiness, reputable manufacturers of differential pressure gauges provide comprehensive technical support and robust warranty policies. This not only assures users of the product's quality but also establishes a long-term relationship based on reliability and continuous support.
As industries continue to evolve with technological advancements, the role of differential pressure gauges becomes even more critical. Their contribution to operational precision, safety compliance, and efficiency improvement makes them an indispensable tool. By understanding their operation, applications, and selection criteria, users can harness the full potential of these devices to optimize their processes effectively.