Differential pressure gauges equipped with a 1/2 NPT connection are crucial in various industrial applications, offering precise pressure monitoring between two points in a system. This specificity allows for efficient detection of pressure drops, which is vital for maintaining system integrity and safety. As you delve into the nuances of these devices, it’s important to explore their practical applications, technical considerations, and reliability.
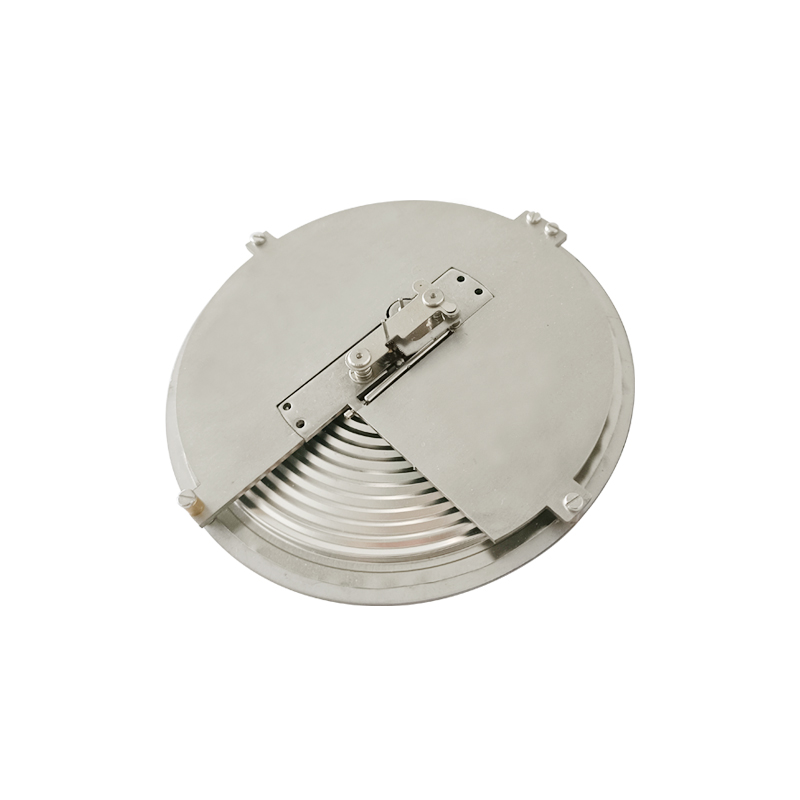
Emphasizing real-world experience, differential pressure gauges play an indispensable role in the oil and gas industry. These industries often operate under strenuous conditions, where monitoring pressure changes ensures the safe and efficient operation of machinery. For example, in filtration systems, a differential pressure gauge can accurately determine when a filter is clogged or needs replacement. This proactive maintenance approach not only saves time but also prevents costly downtime, enhancing system reliability.
The expertise one requires to leverage differential pressure gauges is notable. These devices typically involve intricate mechanics and understanding of the principles of differential pressure measurement. A 1/2 NPT (National Pipe Thread) connection signifies a standardized method, ensuring seamless integration into existing systems. The NPT threading, recognized for its tapered design, provides a reliable and leak-free connection, essential for systems under high pressure.
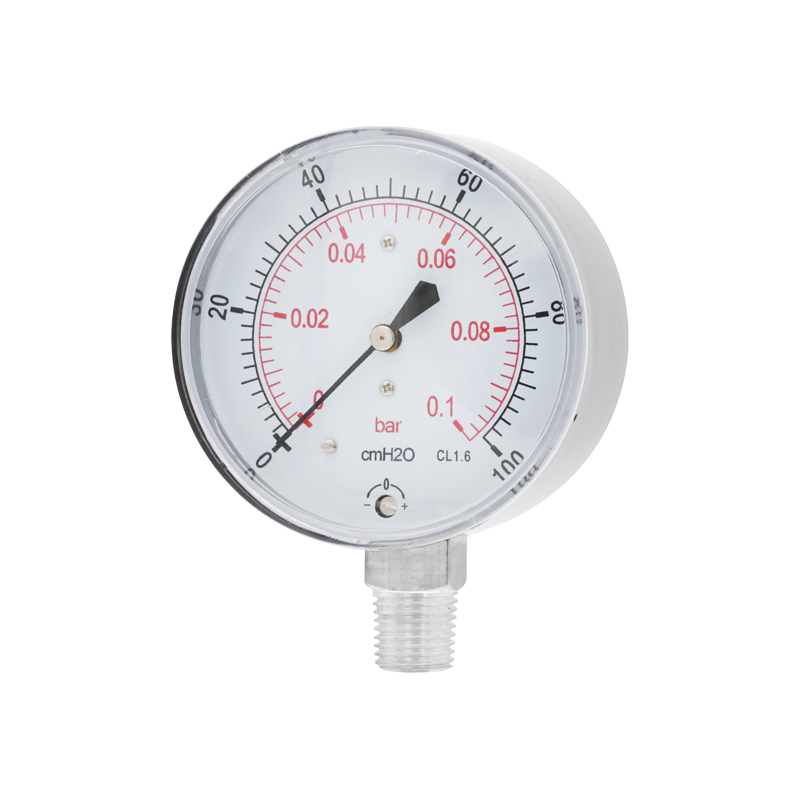
In terms of authoritativeness, differential pressure gauge manufacturers adhere to strict industry standards, such as the ISO 9001 certification, to ensure product reliability and accuracy. Such gauges are rigorously tested for performance in extreme environments, further underscoring their dependability. Manufacturers often collaborate with industry experts to continuously refine product designs, keeping up with technological advancements and user needs.
Trustworthiness in differential pressure gauges is derived from both their construction and the credibility of the manufacturers. High-quality materials, such as stainless steel and corrosion-resistant components, are often employed, ensuring longevity and durability even in harsh environments. End-users often rely on the reputations of established manufacturers who provide comprehensive support and warranties.
differential pressure gauge 1 2 npt
When selecting a differential pressure gauge with a 1/2 NPT connection, several factors should be considered. These include the pressure range, the media compatibility, temperature conditions, and mounting options. For instance, choosing a gauge with the appropriate pressure range prevents damage to the gauge and inaccurate readings. Media compatibility is just as important; gauges must be resistant to the particular fluids or gases they will be monitoring to avoid degradation of internal components.
Temperature variations can affect gauge performance, so it’s crucial to select one with suitable thermal compensation. In extremely cold or hot environments, specific seals and diaphragms may be required to maintain accuracy. The 1/2 NPT connection aids installation, allowing for easy integration and ensuring that the gauge remains firmly in place even under pressure fluctuations.
Furthermore, technological enhancements in digital differential pressure gauges offer improved precision and data recording capabilities. These digital variants can communicate with control systems, providing real-time analytics and integration into comprehensive monitoring frameworks. Such innovations push the boundaries of traditional gauges, offering enhanced features like remote monitoring and automated alerts.
In industrial processes where safety and efficiency are paramount, investing in high-quality differential pressure gauges with a 1/2 NPT connection can significantly impact operational outcomes. They not only provide critical insights into system performance but also contribute to overall safety and cost efficiency. By understanding the specific needs of your application and selecting the appropriate solution, you ensure an optimized and secure process flow, reflecting best practices in operational reliability.
In conclusion, the expertise, experience, authoritativeness, and trustworthiness associated with differential pressure gauges make them vital components in modern industry. Whether in manufacturing, energy production, or chemical processing, their role in ensuring system efficacy cannot be overstated. As technology progresses, these gauges continue to evolve, meeting the demands of increasingly sophisticated industrial environments.