Differential pressure gauges have become crucial instruments in various industries due to their ability to measure the pressure difference between two points. In the realm of engineering and industrial processes, a differential pressure gauge, specifically measured in PSI (pounds per square inch), plays a pivotal role in ensuring not just operational efficiency but also safety and compliance. This article delves into the significance, application, and expertise required to utilize differential pressure gauges effectively, adding a layer of credibility and authority to your understanding.
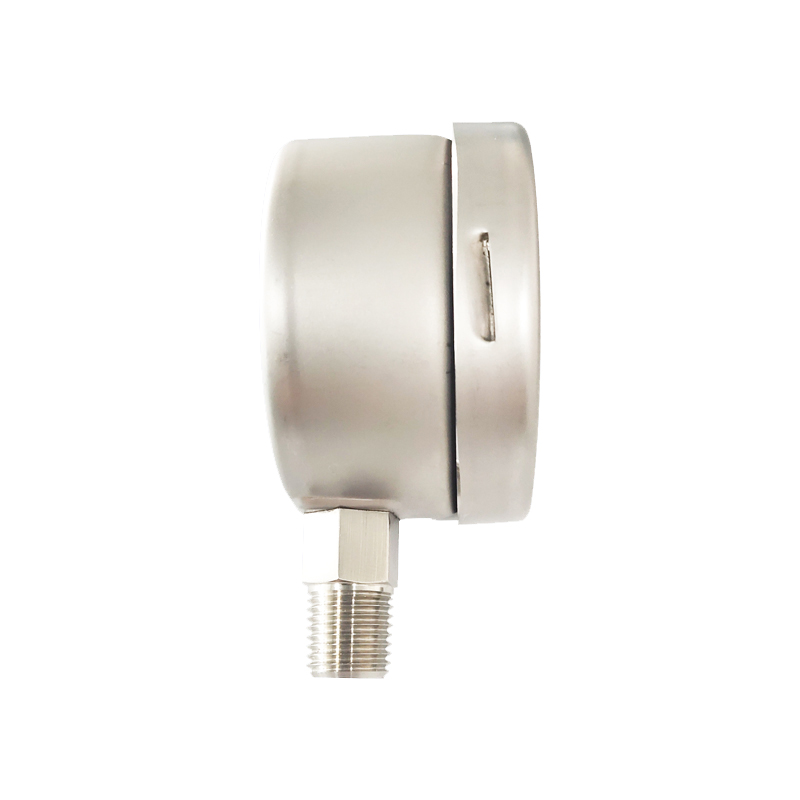
The essence of a differential pressure gauge lies in its ability to provide real-time data about the pressure difference, which is critical in systems where precision is paramount. For example, in HVAC systems, maintaining optimal air pressure is necessary for energy efficiency and environmental comfort. An accurate PSI reading from a differential pressure gauge can prevent system overloads and inefficiencies, reducing energy consumption and operational costs.
Expertise in using these gauges involves understanding the various types available, such as piston, diaphragm, or bellows types, and selecting the right one for your specific application. Each type has its strengths—piston gauges are known for durability in high-pressure environments, while diaphragm gauges offer better sensitivity for low-pressure applications. Selecting the correct type and range, often between 0.25 to 100 PSI for standard industrial applications, is crucial. Consulting with manufacturers or employing experts in fluid dynamics can enhance decision-making, ensuring the selected gauge meets the technical requirements of your application.
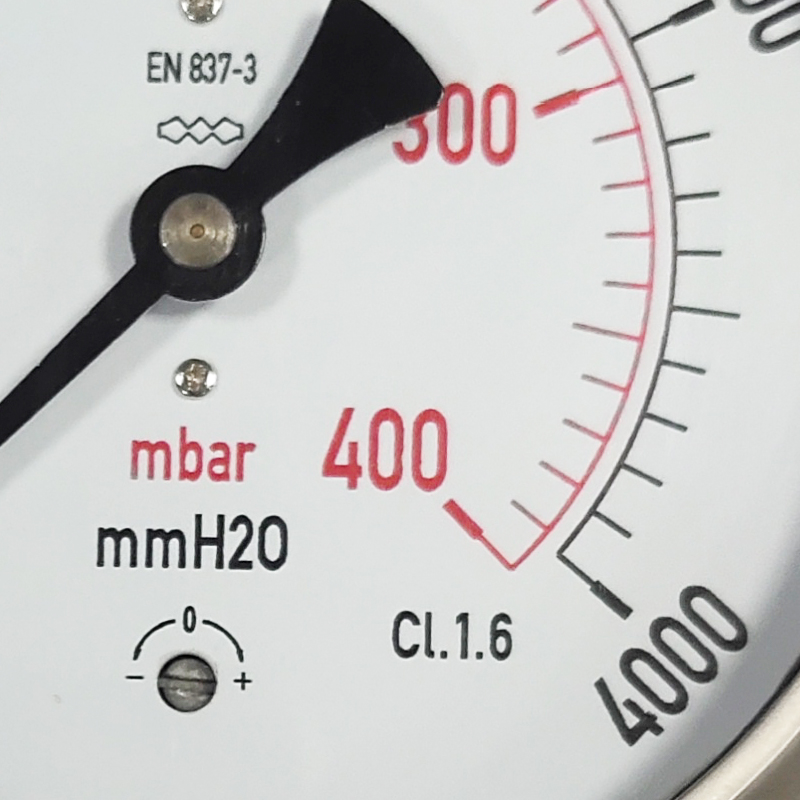
Accurate installation and maintenance are equally vital components in maximizing the operational life and reliability of a differential pressure gauge. Incorrect installation can lead to false readings, which can cascade into larger issues such as equipment failure or safety hazards. Thus, consulting installation manuals, or ideally, enlisting trained professionals for setup can mitigate these risks. A well-maintained gauge needs periodic calibration, a process that ensures the readings remain accurate over time. Calibration involves comparing the gauge's output with a standard reference, adjusting it if necessary to match the reference values. Undertaking this task at regular intervals, ideally annually, can preserve measurement integrity.
differential pressure gauge psi
In the realm of authority and trustworthiness, relying on brands with a well-established reputation in precision instruments can offer peace of mind. Brands that comply with international standards, such as ISO 9001 for quality management, signify reliability and guarantee that the instruments have undergone rigorous testing. User reviews and case studies can also provide insight into real-world performance and reliability, building trust through community validation.
An often overlooked aspect is the digital transformation of differential pressure gauges. Modern developments have integrated digital displays and connectivity features that allow for real-time data monitoring remotely. This evolution has made it easier for operators to receive alerts and react promptly to any discrepancies in pressure readings. For an even more sophisticated setup, these digital gauges can be integrated into a broader IoT ecosystem, offering predictive maintenance insights, which enhances both the efficiency and lifespan of equipment.
Finally, possessing comprehensive knowledge and understanding of local regulations concerning pressure measurement is imperative. Many industries have stringent regulations about operational safety, environmental compliance, and energy usage, all of which can be influenced by the precise measurement of differential pressure. Instruments that offer data logging capabilities can prove invaluable for audit trails and compliance reporting.
In conclusion, differential pressure gauges are indispensable tools in monitoring and maintaining system integrity across various industries. Their precise PSI readings ensure protection against system failures and guide energy-efficient operations. By selecting the appropriate type, ensuring precise installation and maintenance, leveraging modern digital capabilities, and aligning with regulatory standards, users can significantly enhance their operational reliability and efficiency. This profound understanding not only underscores a commitment to quality and safety but also elevates your authority and trustworthiness in employing these vital instruments.