Understanding the intricacies of industrial instrumentation often requires a deep dive into specific devices, each designed to fulfill a particular role in complex systems. Among these, the bellow type differential pressure gauge stands out as a vital tool widely used across various sectors for its precision and reliability.
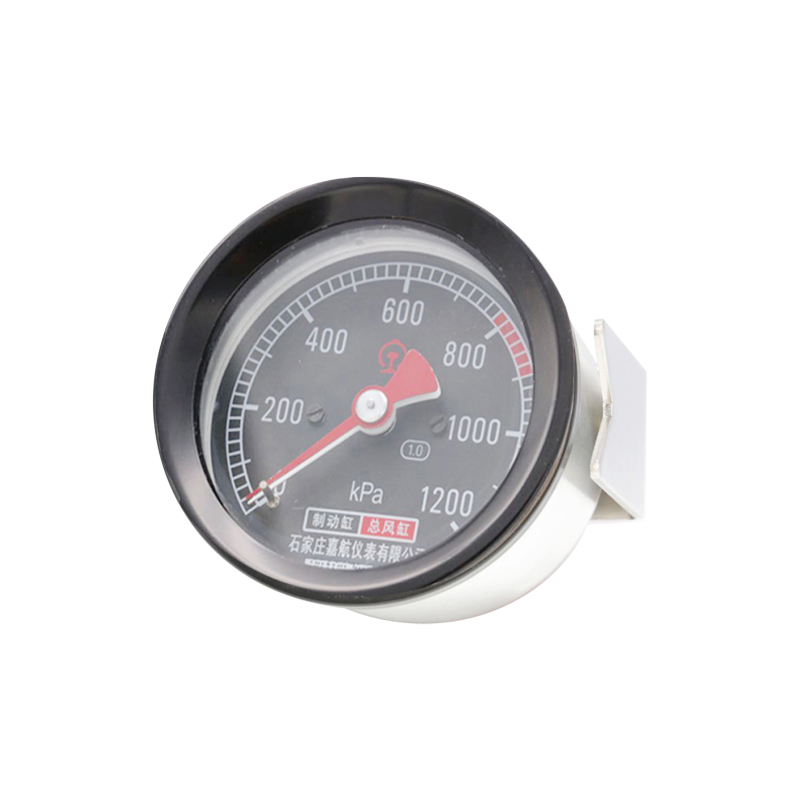
At its core, the bellow type differential pressure gauge measures the difference in pressure between two points within a system. This device is essential in applications where monitoring and maintaining pressure differentials is crucial—for instance, in filtration systems, pumps,
or flow measurement setups. The unique mechanism of the bellow gauge involves a set of bellows, which expand and contract according to the pressure changes, transforming these physical movements into a readable output on the gauge itself.
A testament to its utility in industrial settings, this gauge is particularly renowned for its ability to handle low-pressure differences with high accuracy. Industries dealing with highly sensitive processes, such as pharmaceuticals, food processing, and petrochemicals, often rely on these devices for maintaining operational integrity and safety. The precision offered by bellow type differential pressure gauges allows for meticulous monitoring, ensuring processes remain within set parameters and avoiding potentially costly deviations.

The expertise embedded within these devices is evident in their construction and functionality. High-quality materials are used to enhance durability and withstand the harsh conditions often found in industrial environments. Stainless steel is a common choice for the casing, providing robustness and corrosion resistance, which is critical for equipment longevity and reliability. The bellows themselves are constructed from materials like phosphor bronze or stainless steel, chosen for their resilience and consistent performance under repeated cyclical pressure loading.
In the realm of authoritative measurement tools, the bellow type differential pressure gauge is distinguished by its mechanical simplicity and the elimination of electrical components in certain models. This absence of electronics means it offers an intrinsically safe solution for industries prone to explosive atmospheres, further underscoring the gauge's versatility and trustworthiness. Electrical interference and failures are non-issues, making these gauges highly dependable in environments where precision is non-negotiable.
bellow type differential pressure gauge
To authenticate the reliability and trustworthiness of these gauges, industry standards and rigorous testing protocols are followed. Manufacturers of these instruments often adhere to ISO norms and other sector-specific certifications, ensuring that each device not only meets but exceeds the operational benchmarks required by modern industry regulations. This adherence to standardization not only assures performance consistency but also builds a foundation of trust with end-users who rely on these gauges for critical measurements.
Practical experience in employing bellow type differential pressure gauges in real-world settings often reveals their straightforward installation and maintenance benefits. Unlike more complex systems, these gauges typically require minimal training and expertise to set up and operate. The intuitive nature of the analog readouts means that operators and engineers can quickly interpret data without the need for extensive analysis or digital interfaces, expediting decision-making processes in fluid or dynamic operational contexts.
Furthermore, maintenance routines are simplified by the very design of these instruments. Regular inspection of mechanical components and calibration ensures continued high performance, with minimal downtime expected. When maintenance is required, the modular design allows for straightforward part replacements or repairs, often achievable with standard tools and without the need for specialized knowledge. This accessibility not only reduces overall operation costs but also empowers on-site teams to maintain the gauges effectively.
Investing in a bellow type differential pressure gauge is a decisive move toward enhancing operational efficiency and safeguarding process integrity. By providing clear, accurate measurements of pressure differentials, these gauges help prevent equipment fouling, optimize filtering processes, and maintain flow consistency—all critical factors that contribute to overall system performance. Their role in ensuring operational excellence cannot be overstated, and their value continues to be recognized in sectors where precision engineering is paramount.
Overall, the enduring popularity of bellow type differential pressure gauges is a reflection of their unparalleled combination of precision, reliability, and ease of use. In a landscape where advancing technology often steers toward complexity, these gauges stand as a testament to the effectiveness of simple yet robust design. For industries seeking an authoritative measurement solution backed by real-world efficacy and longevity, the bellow type differential pressure gauge remains an indispensable choice.