In the intricate world of industrial applications, precision and reliability are the cornerstones of success. A differential pressure gauge with a sealed capillary is an epitome of this precision—an essential tool that ensures stability, safety, and efficiency in various processes. Here, we delve into the nuances of this specialized equipment, sharing insights from industry experts and real-world applications that solidify its standing as a critical component in industrial settings.
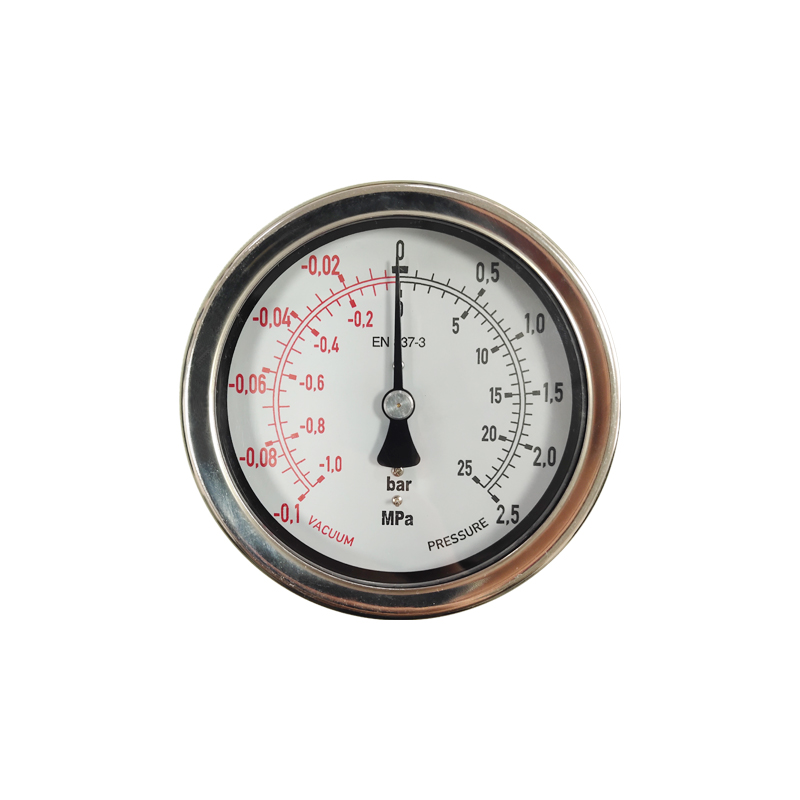
Differential pressure gauges are indispensable in scenarios where monitoring the pressure difference between two points is crucial. The addition of a sealed capillary in these gauges transforms their functionality and applicability. A sealed capillary system is essentially a length of tubing filled with a transmission fluid, providing a pathway for pressure readings from a remote site to the gauge. This design feature elevates the differential pressure gauge from a simple monitoring tool into a sophisticated instrument capable of performing under stringent conditions.
One of the biggest advantages of a differential pressure gauge with a sealed capillary is its ability to perform in extreme environments. Equipped to withstand harsh temperatures, vibrations, and corrosive substances, these gauges are the go-to choice for industries such as chemical processing, oil and gas, and pharmaceuticals. By isolating the pressure sensor from the process fluid through the capillary and seal, measurement accuracy is maintained while protecting sensitive components from potential damage.
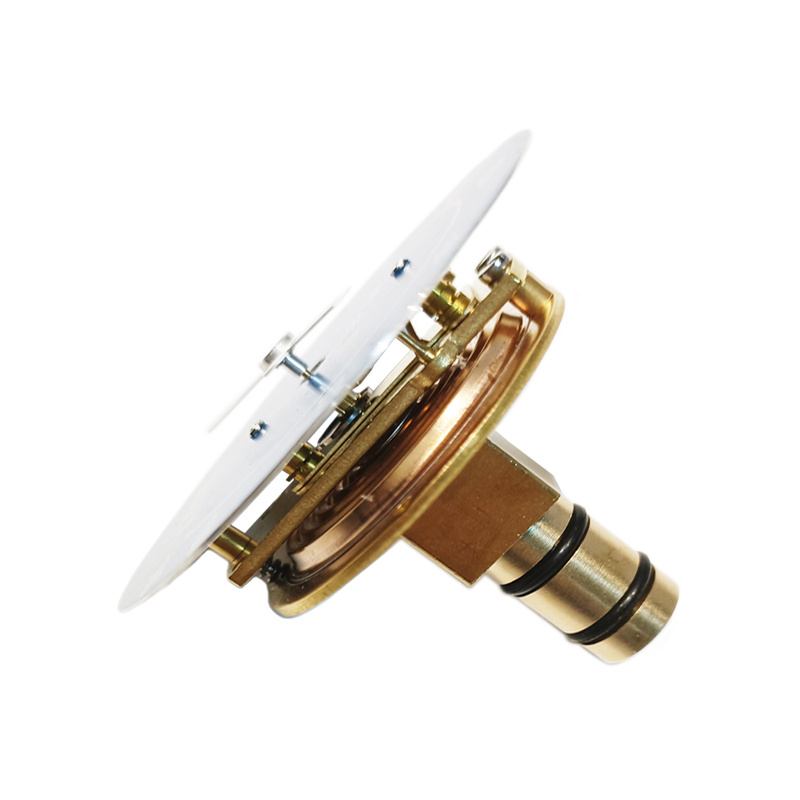
Renowned industry expert, Dr. Emily Tran, who has over 20 years of experience in fluid dynamics and instrumentation, emphasizes the importance of accuracy and durability. In high-stakes industries, there's no room for error. A sealed capillary system in these gauges ensures precise readings by maintaining the integrity of the sensor, which is paramount for process optimization and safety, she explains.
Not only do these gauges offer protection in aggressive environments, but they also ensure reliability in remote or inaccessible locations. Traditional pressure gauges often face challenges in such settings due to environmental factors or physical constraints. However, with a sealed capillary, the gauge can be mounted at a safe or easily accessible location, while the remote sensing point remains embedded within challenging environments. This capability enhances operational efficiency by simplifying maintenance and reducing downtime.
differential pressure gauge with sealed capilary
Users who have integrated these gauges into their operations consistently report enhanced process control and reduced maintenance needs. Mark Rosenthal, operations manager at a leading petrochemical company, shares his experience After switching to differential pressure gauges with sealed capillaries, we've noticed a significant drop in maintenance intervals. The setup not only offers reliable data but also reduces the wear and tear on our equipment.
The expertise involved in manufacturing these gauges also adds to their reliability. Only a few manufacturers globally have mastered the production of sealed capillary systems, reflecting the specialized knowledge required. These manufacturers adhere to stringent quality control measures, ensuring each unit meets the highest standards of precision and durability.
Trustworthiness in these instruments is further bolstered by comprehensive testing protocols. Before reaching the end-user, these gauges undergo rigorous testing to ensure performance across various pressures and temperatures. This ensures that every gauge delivers consistent and accurate readings, fostering confidence among users who depend on them for critical operations.
In conclusion, a differential pressure gauge with a sealed capillary offers an unparalleled blend of precision, durability, and reliability. It stands as a testament to advanced engineering, meeting the demanding needs of modern industries. By opting for such gauges, businesses not only enhance their operational capabilities but also align with a standard of excellence that reflects their commitment to safety and efficiency. Trust in this technology is well-placed, given its track record of performance and innovation.