Cryogenic differential pressure gauges, or OEM cryogenic differential pressure gauges, are vital instruments for industries that require precise pressure measurements under extremely low-temperature conditions. These specialized gauges find applications in various sectors, including LNG (liquefied natural gas) processing, cryogenic storage tanks, and laboratory research involving liquid gases.
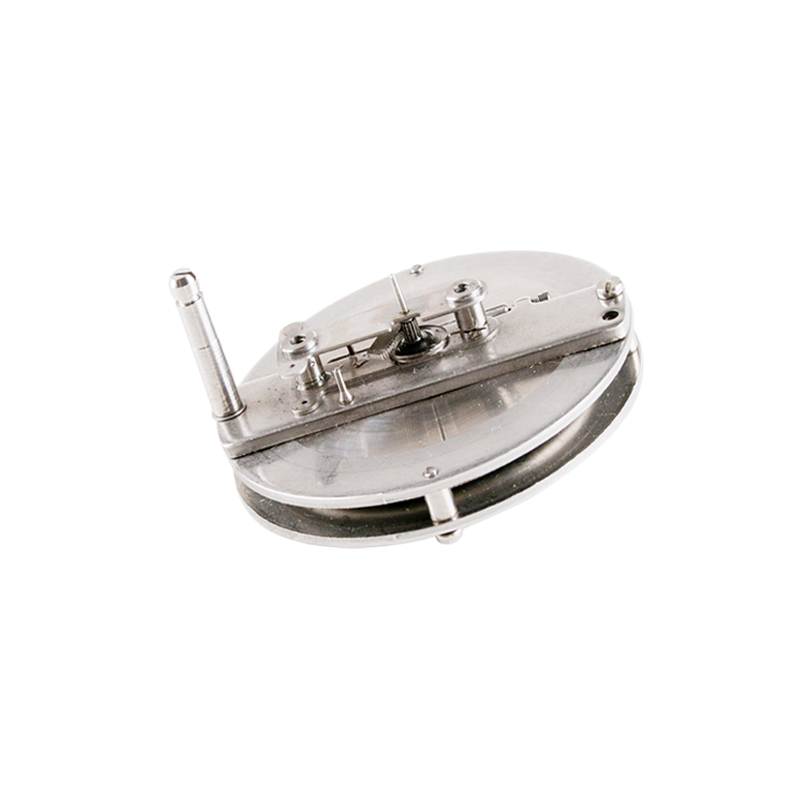
The primary function of a cryogenic differential pressure gauge is to measure the difference in pressure between two points within a system. This is crucial for maintaining system balance and ensuring the safe and efficient operation of processes that involve cryogenic liquids. Such operations often entail handling gases like liquid nitrogen, helium, or oxygen, where traditional pressure measurement tools may fail due to the extreme cold.
Experience shows that the key to utilizing these gauges effectively lies in understanding the unique challenges posed by cryogenic environments. The materials used in the construction of these gauges, including stainless steel and specialized elastomers, are selected for their ability to withstand extreme temperatures without compromising accuracy or performance. Users have observed that neglecting these specifications can result in inaccurate readings or even gauge failure, which can lead to costly and dangerous operational mishaps.
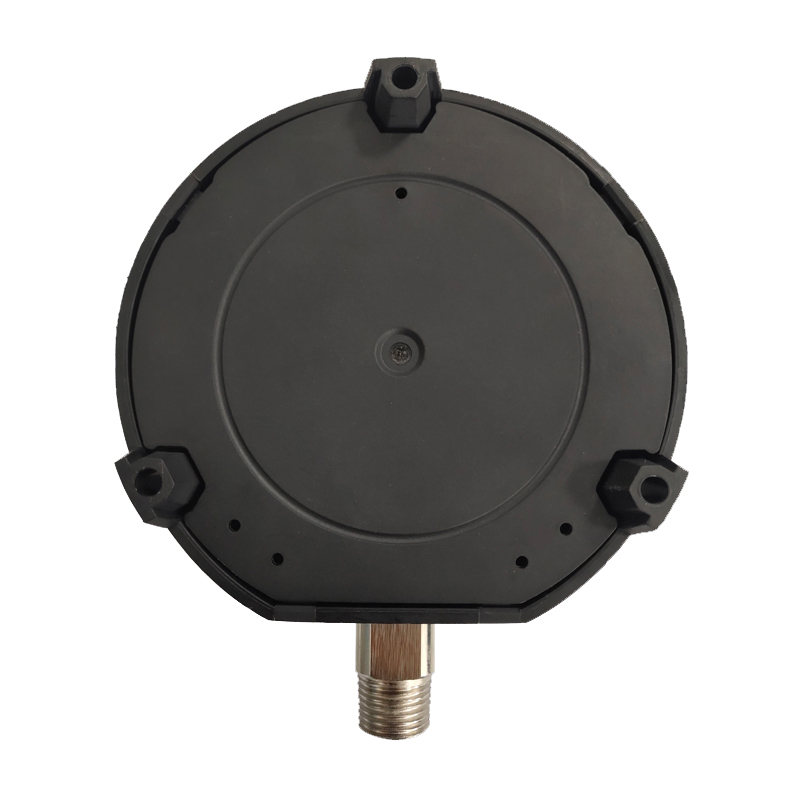
From an expertise standpoint, manufacturers of OEM cryogenic differential pressure gauges build on years of engineering and field experience to produce reliable instruments. These devices often incorporate advanced features such as temperature compensation elements and robust diaphragm sensing technology. Engineers emphasize the need for integration with compatible systems, considering the unique requirements of each cryogenic process to ensure compatibility and accuracy.
Authoritativeness in the realm of cryogenic differential pressure gauges is established through rigorous testing and standards compliance. Leading manufacturers subject their products to extensive thermal testing cycles to validate their performance under various operating conditions. Adherence to international standards such as ASME, ISO, or ANSI not only enhances trust in these gauges but also confirms their suitability for critical applications. Professionals in the field consistently highlight the importance of selecting devices that meet these standards to ensure the longevity and dependability of the equipment.
oem cryogenic differential pressure gauge
Trustworthiness is further reinforced by the continuous improvement of technology based on user feedback and innovation. Companies invest heavily in research and development to refine the performance characteristics of their cryogenic differential pressure gauges. Industry experts recommend prioritizing gauges from manufacturers who offer comprehensive support, including technical assistance and warranty services, as these elements significantly contribute to the overall trust in the product.
When deploying OEM cryogenic differential pressure gauges, users must also consider the installation environment. Proper insulation and positioning of the gauges are essential to maintain measurement accuracy and device longevity. Experts advise regular maintenance checks to ensure that calibration remains true to specified values, as cryogenic systems can introduce variables that affect precision over time.
Furthermore, experts in the industry understand that the digital transformation is influencing these devices significantly. The latest models often feature integrated digital displays, remote monitoring capabilities, and connectivity with industrial IoT systems. This technological evolution is pivotal for industries aiming to streamline operations and enhance system management through real-time data analysis and remote diagnostics. Selecting OEM cryogenic differential pressure gauges with these modern attributes can dramatically increase operational efficiency and response times during incidents, ensuring a broader safety net and improved decision-making processes.
Ultimately, the optimal choice of an OEM cryogenic differential pressure gauge hinges on a comprehensive understanding of both the technical demands of the application and the operational nuances of cryogenic environments. Professionals emphasize that success in this realm is a blend of selecting the correct product and maintaining it with the precision that cryogenic operations demand. As the capabilities and designs of these gauges continue to advance, staying informed on the latest developments can provide users with a significant edge, ensuring that they leverage the full spectrum of benefits offered by these sophisticated instruments.