The bourdon differential pressure gauge stands as a staple in various industries where precise monitoring and control over pressure differences are critical. These instruments, distinguished by their reliable performance and accuracy, have been integral to processes spanning from HVAC systems to industrial manufacturing. Their design, leveraging the bourdon tube's elasticity, ensures a high level of precision that aids industries in maintaining operational efficiency and safety.
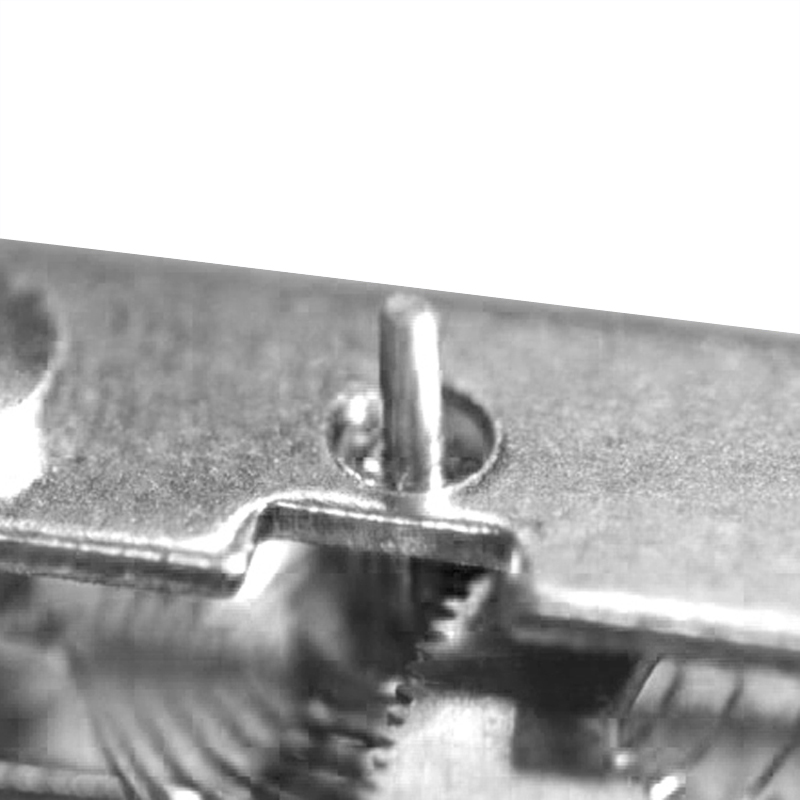
In industry applications like chemical processing plants and oil refineries, the need for precise pressure measurement cannot be overemphasized. These environments rely heavily on bourdon differential pressure gauges due to their robustness and capability to withstand extreme pressure ranges and harsh conditions. Their design is engineered to resist factors such as corrosive substances and high-temperature fluctuations, making them a trusted choice for professionals seeking durable solutions.
One of the most compelling aspects of bourdon differential pressure gauges is their mechanical simplicity combined with measurement efficiency. These gauges consist of two bourdon tubes, each connected to the respective ports between which the pressure differential is being measured. The mechanical movement of these tubes is translated through a rod and gear mechanism that indicates the pressure differential on a calibrated dial. This simple yet effective mechanism assures users of minimal maintenance, enhancing the trust in their long-term performance.
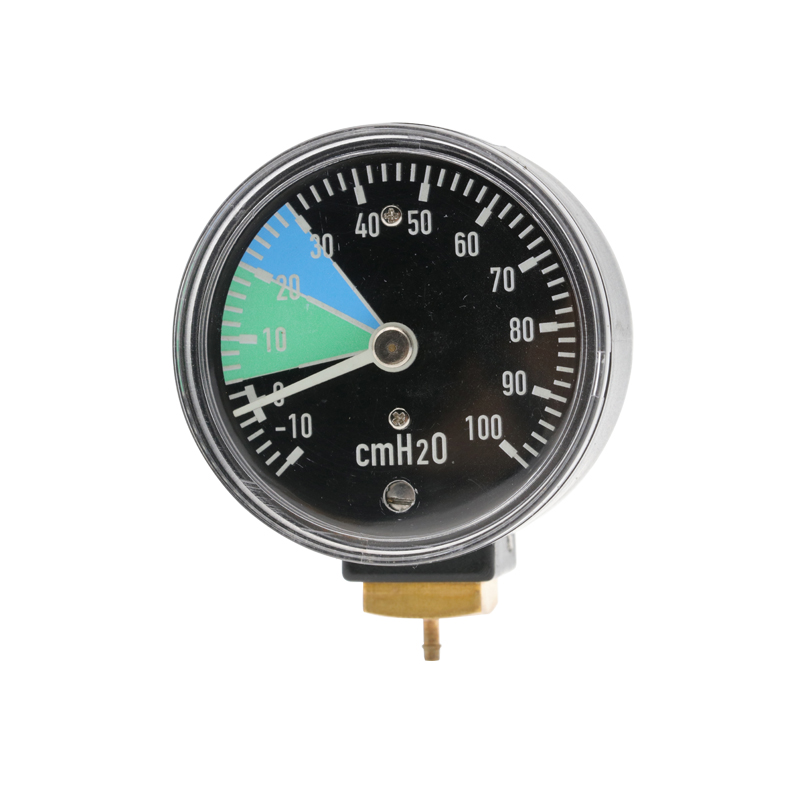
From an expertise standpoint, understanding the intricacies of how a bourdon tube operates provides deeper insights into why these gauges are favored. The bourdon tube, typically a thin-walled metallic coil,
expands and contracts with pressure fluctuations. This movement is then amplified by a gearing system which translates the mechanical motion to a dial face, depicting accurate pressure readings. This mechanism offers not only high reliability but also reduces potential error that can arise from digital systems, which can be prone to electronic malfunctions in high-demand environments.
bourdon differential pressure gauge
The authority of bourdon differential pressure gauges also lies in their adaptability. These gauges can be customized with various materials and designs to fit specific industry requirements, enhancing their effectiveness. For instance, in industries where highly corrosive materials are present, gauges can be coated or constructed from specialty alloys to extend their lifespan and reliability. These modifications are critical for engineers who need precise control to ensure that systems operate within their designated safety parameters.
Furthermore, bourdon differential pressure gauges are deeply trusted due to their proven track record over years of usage. Their mechanical nature makes them less susceptible to issues that might affect digital or more sophisticated electronic gauges, thereby providing a more trustworthy and dependable measurement. This trust is critical in scenarios where failure to monitor pressure could lead to catastrophic results, such as in the management of steam pressure in boilers.
Incorporating bourdon differential pressure gauges into a system also enhances safety protocols effectively. By providing precise pressure measurements, these gauges help identify potential leaks or blockages within systems, acting as an early warning system that enables timely maintenance and prevention strategies. For industries aiming to meet stringent safety regulations, the integration of trustworthy instruments like bourdon differential pressure gauges is paramount.
In summation, bourdon differential pressure gauges offer an exemplary blend of precision, reliability, and adaptability that makes them indispensable to a multitude of industries. Their robust construction ensures resilience against demanding operational environments, while their mechanical simplicity aids in minimizing maintenance. For industries seeking to enhance operational safety and efficiency, the bourdon differential pressure gauge remains a definitive choice that continues to stand the test of time.